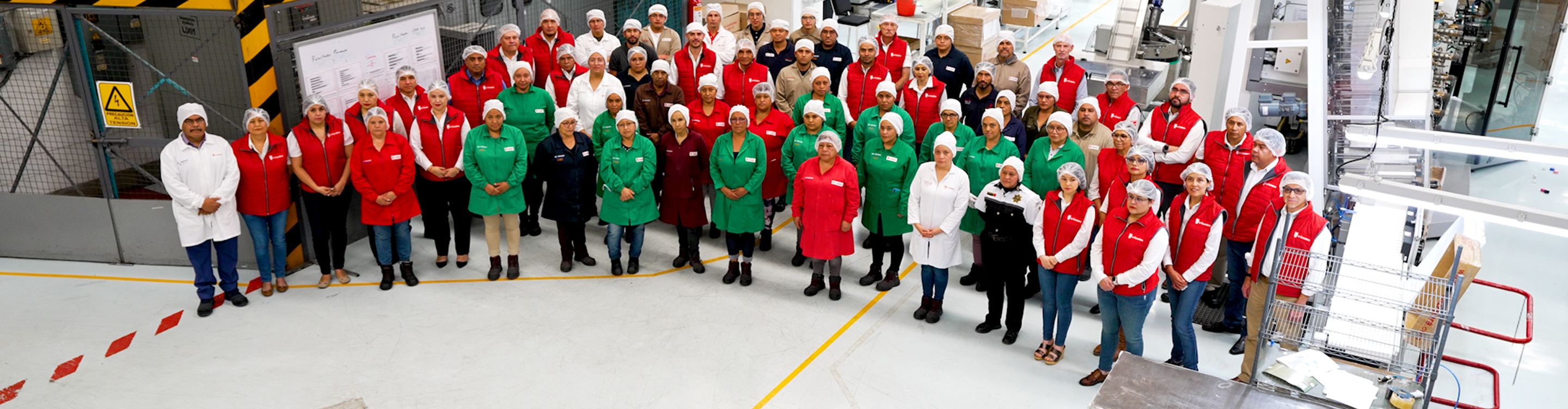
A Transformative Vision: How La Cazadora Digitized Their Shop Floor with Pulsar
Discover how Pulsar helped La Cazadora gain better visibility into its industrial operations, generate agile reports, and align all departments around production.
The Challenge
With over 80 years of experience, La Cazadora has established itself as a leader in the manufacturing of plastic squeeze tubes for the personal care, food, cosmetics, and pharmaceutical industries. They have an installed capacity of over 160 million tubes per year, and their clients include some of the world's most well-known brands. Since they handle a highly specialized and custom product, both agility and quality are essential throughout their production processes, which include extrusion, head assembly, printing, and packaging.
La Cazadora had sought out solutions and techniques to help improve its operations on several occasions. Their production processes required constant coordination between Production, Maintenance, and Quality. Production start times were often somewhat lengthy, and when a critical machine issue arose that needed support, it could take other departments more than 60 minutes to determine what had happened on the shop floor.
Overall, visibility and communication regarding the causes of downtimes and critical events were limited to weekly coordination meetings. Daily operations used manual logging for downtime tracking—with unique paper logs for each machine—that didn't allow for simultaneous collaboration and required manual work and transcription to generate reports.
La Cazadora needed greater visibility into its operations and to digitize its processes. With this plan in mind, they decided to invest in a technological solution that would allow them to evolve to the next level.
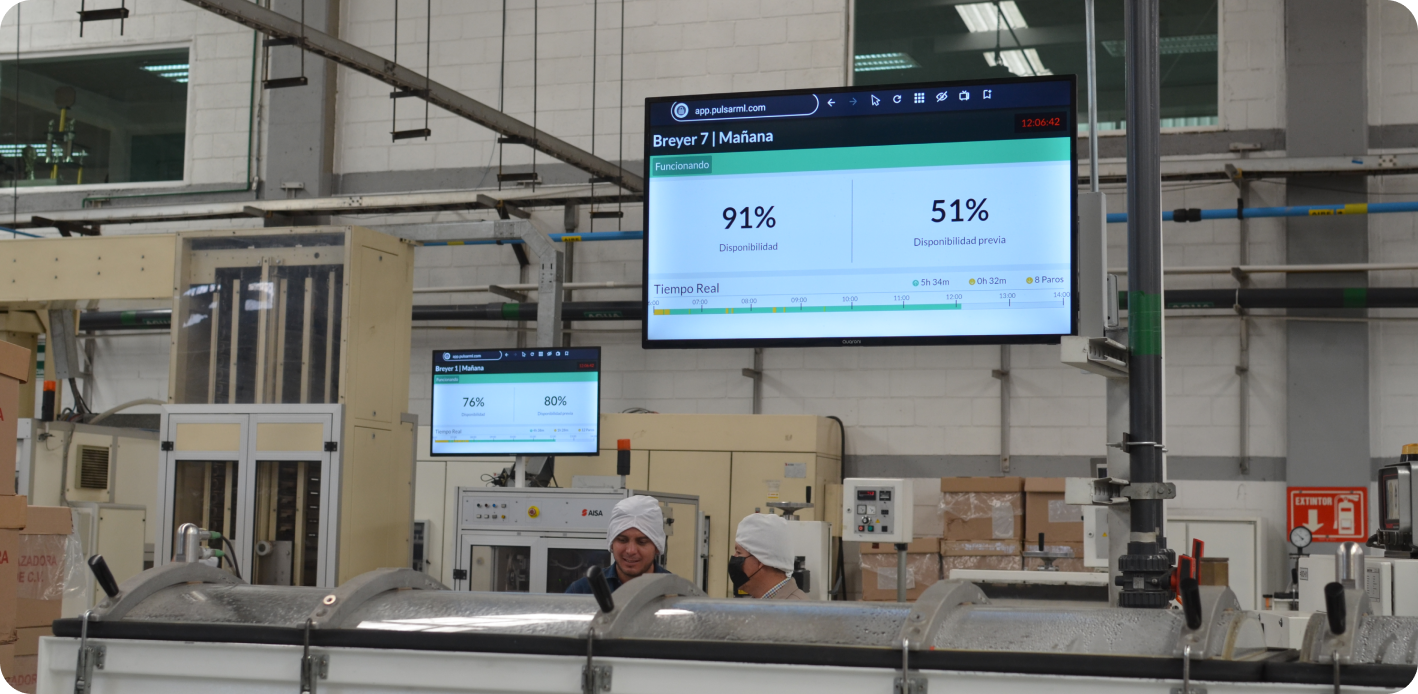
The Solution
La Cazadora implemented Pulsar on 17 critical machines, equipping them with screens that leverage the platform's TV mode, which displays key productivity indicators in real-time. The company assigned a tablet to each operator for digitally classifying downtimes, and granted access to the platform to all departments. Additionally, an extra screen was installed at the entrance of the production area, visible to everyone.
“It's a very visual interface for everyone, and it shows the status of each line. We've reduced the time spent processing written information from paper to Excel to prepare weekly production reports. We've also fostered healthier competition between production lines.”
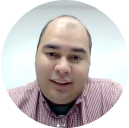
Management actively promoted the adoption of Pulsar at all levels of the company. The platform began to automatically register downtime and other key metrics. This new practice enabled the replacement of La Cazadora’s manual downtime logging with Pulsar’s reports.
Just weeks after adopting the platform, the team began to notice the technology’s impact on their plant:
- The Production, Quality, and Maintenance departments utilized the platform to gain real-time visibility into situations that required attention.
- Supervisors leveraged automated reports, eliminating the need for manual transcription and data cleaning.
- All departments implemented smartphone alerts to receive instant notifications about machine stoppages.
- Thanks to the screens, operators could now view their productivity and access information from all shifts.
Real-time machine monitoring
TV mode for shop floor monitoring
Instant downtime alerts
Data collection and analytics for production planning
Results
One year after implementing Pulsar, La Cazadora has become a much more agile company with better coordination. Now, all departments are aware of what’s happening across all three shifts in real-time, no matter where they are. Weekly meetings use Pulsar’s numbers as a baseline, enabling greater agility and clarity in planning.
The impact of bringing visibility to their operations was clear and powerful:
- They gained greater precision and clarity about machine downtimes and their causes, enabling faster corrective actions.
- They reduced confusion, errors, and information gaps across all three shifts.
- They cut the time spent creating daily production reports and weekly planning meeting reports by 75%.
- Increased reliability of time tracking improved the recording of production start times, resulting in a 20% reduction.
- They boosted competitiveness among their machine operators, who now closely track their progress toward performance goals.
By digitizing the shop floor with Pulsar, La Cazadora has fostered a culture of proactivity, focusing its meetings on continuous improvement and tracking initiatives, rather than just validating information. This project has enabled departments to support one another and remain fully aligned in daily operations. With improved data, production incentives were also adjusted to reflect the reality of productive time.
Driven by Pulsar and its transparency in operations, La Cazadora reaffirms its commitment, vision, and technology to deliver high-quality products to the world's most recognized brands.
Overall Benefits
Explore our platform
Explore more success stories
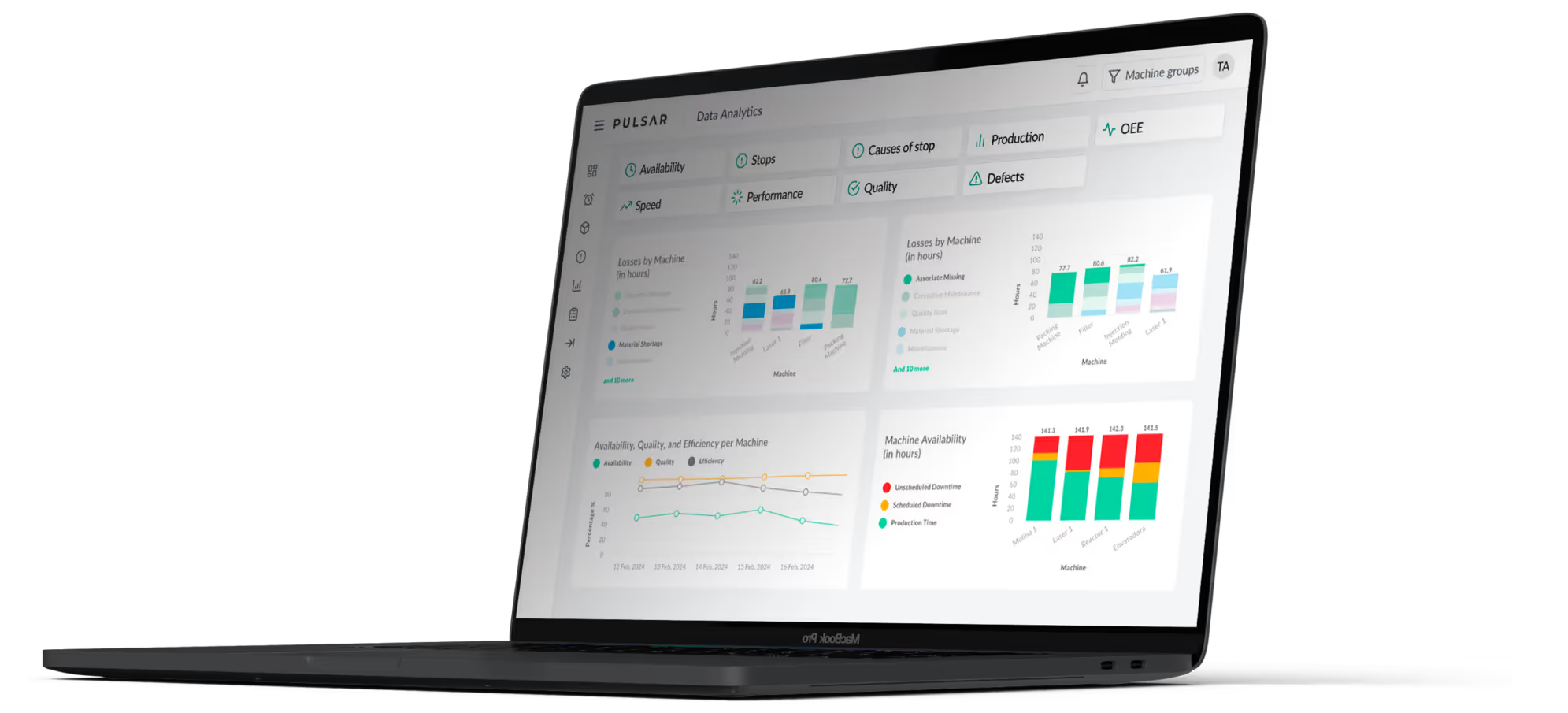
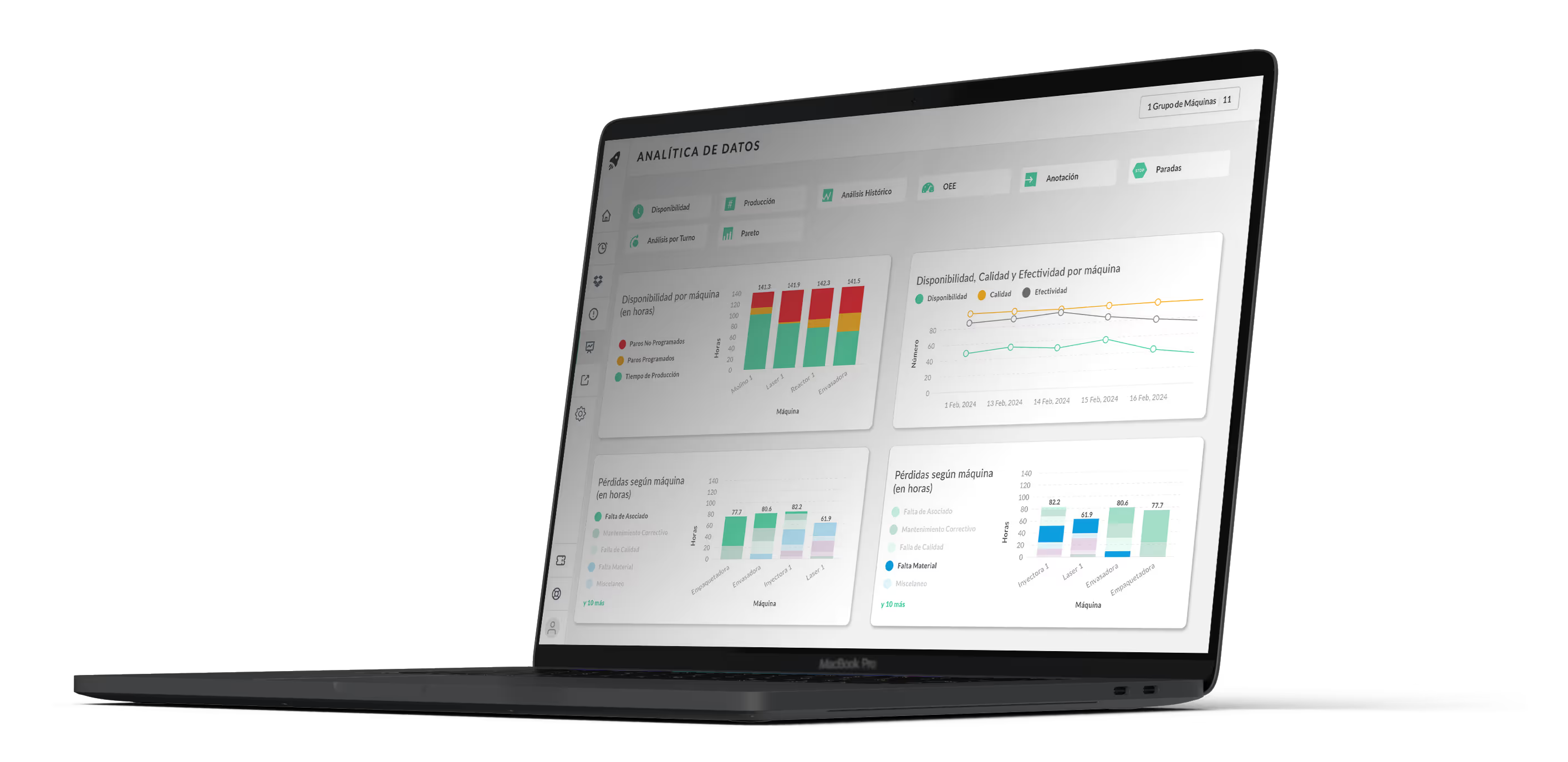
Request a Custom Demo
See how Pulsar’s OEE machine monitoring can help your operations today.
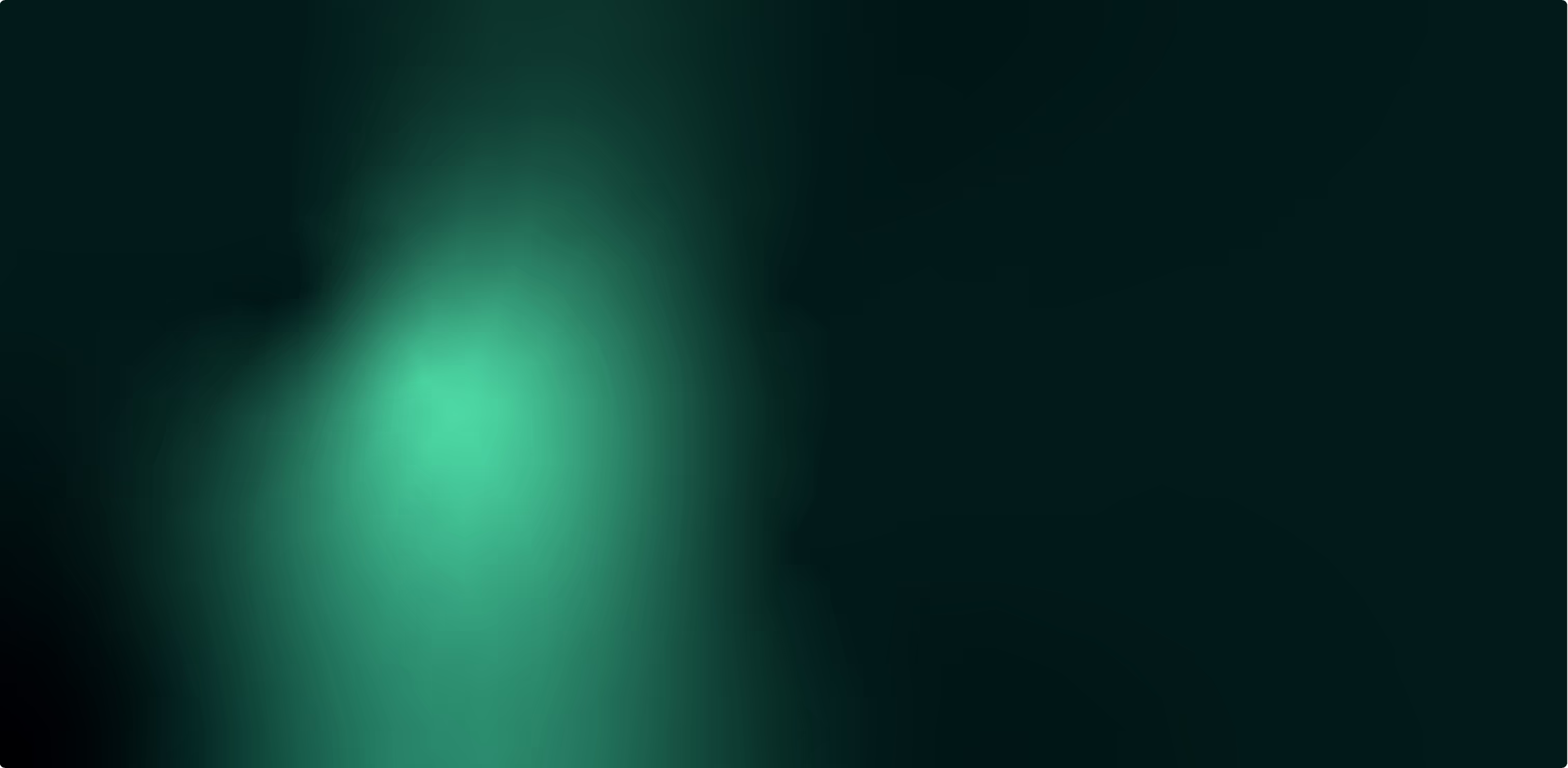