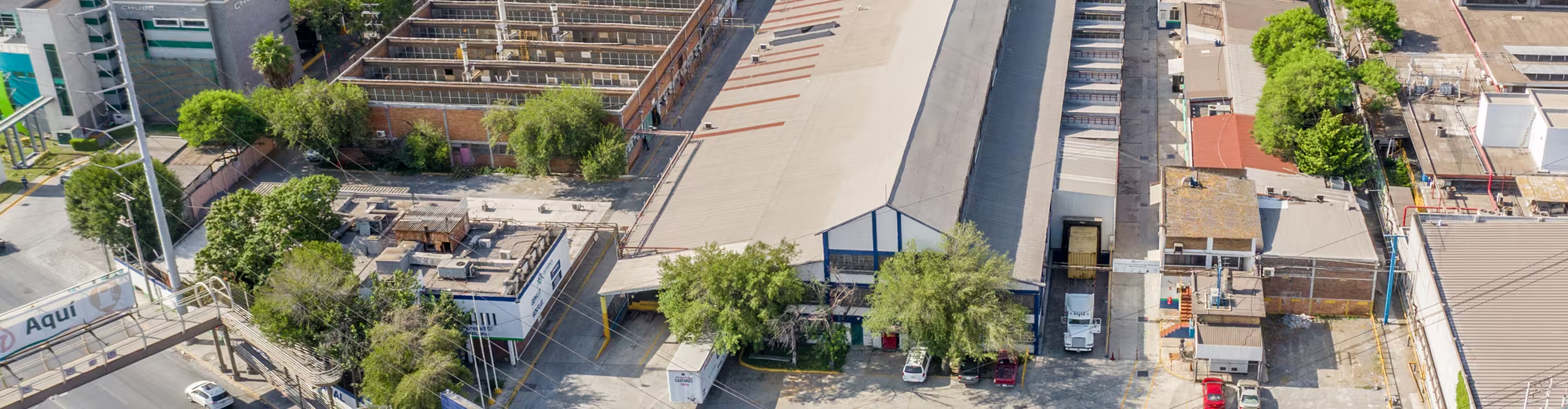
Taking Back Control: How Genvamex Transformed Its Operations with Pulsar
Learn how Genvamex transformed its operations by implementing Pulsar as part of its daily processes to address the sudden increase in work orders.
The Challenge
After a long history as specialists in hinges, padlocks, and locks, Genvamex made the decision to offer metalworking services to the industry. In 2022, they began to offer metal stamping, electroplating, electrostatic powder coating, and zamak injection services, as a response to the challenges of the pandemic and the increasing competition from the Asian market.
A little over a year after this decision, the company faced a production challenge: one of its high-volume clients requested many orders for stair parts. This caused a bottleneck in the metal stamping press area and led to delays in fulfilling orders.
The metal stamping process accounted for 80% of the company's total production, manufacturing up to 2 million parts per month. It was difficult for the Genvamex team to address this challenge because they used manual records of their machine stops. Generating reports and charts was very time-consuming, and as a result, they lacked clarity on the causes of their downtime. Often, the information in their manual reports was incomplete or contained errors.
Driven by their commitment to their clients, the company decided to transform its operations by implementing Industry 4.0 technologies.
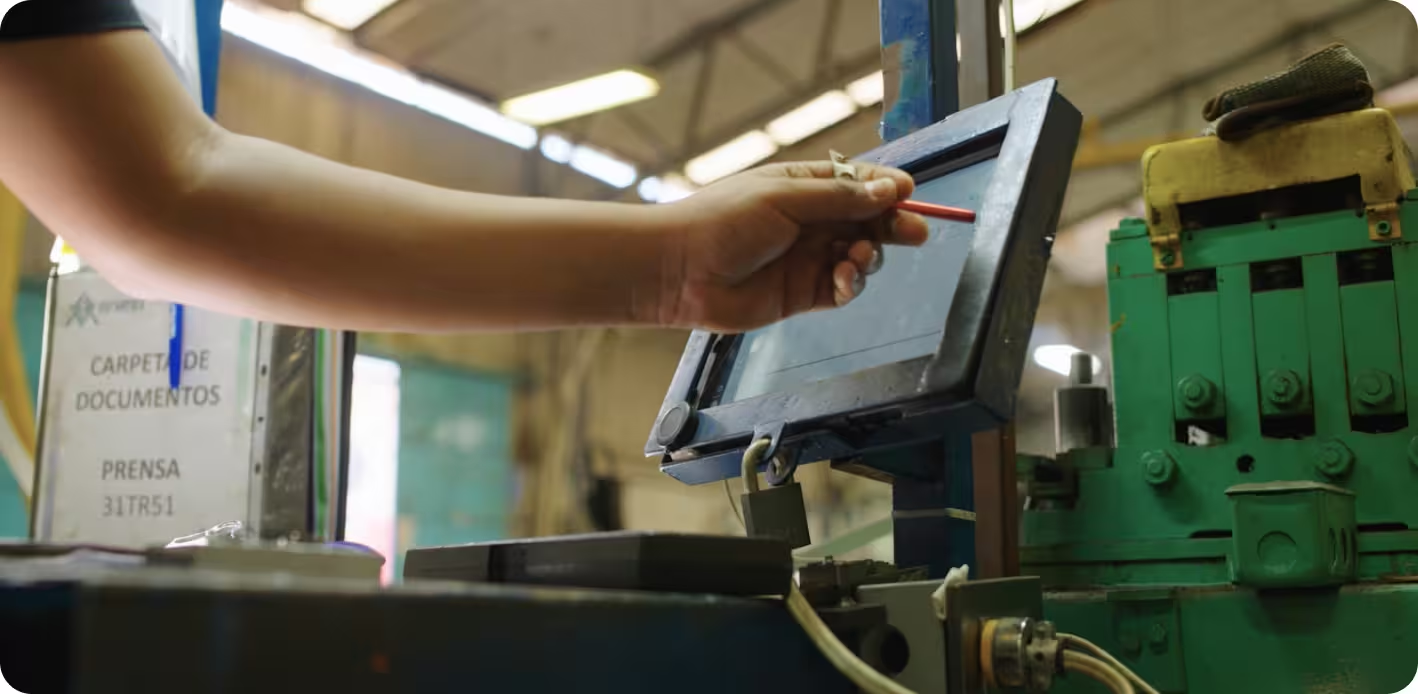
The Solution
Genvamex implemented Pulsar as its industrial monitoring platform on the 12 metal stamping presses dedicated to the stair client's project. Using Pulsar's industrial sensors, the installation was quick and integrated presses of various types and tonnages.
The process and production areas began using Pulsar for real-time indicator monitoring and for generating reports with their operational data. Both operators and managers adopted the platform relatively quickly, achieving the first results in less than a month.
“Today, we can have a better operating condition based on the metrics that this platform offers us, which translate into savings that are passed on to our customers.”
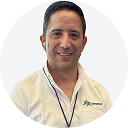
Leveraging real-time data and automated production reports provided by Pulsar, they made significant adjustments in the press area:
- Die re-engineering
- SMED (Single-Minute Exchange of Die) Implementation
- Optimization of material setup
- Roll change optimization
In addition, they implemented the DMAIC (Define, Measure, Analyze, Improve, and Control) methodology for their operations, driving improvement with Pulsar's precise indicators of the processes they sought to improve.
Real-time monitoring of productivity indicators
TV mode for plant monitoring and digital Andon system
Downtime detection and cause logging
Downtime alerts via email and WhatsApp
Automated daily reports
Results
In one year, the Genvamex team managed to transform their operations using Pulsar and made significant improvements in their production. Some of their results from optimizing their processes using the platform:
- Improved efficiency of the metal stamping press process, going from 2 shifts to just 1.
- Identified downtime due to material setup and achieved an 80% reduction in time using the SMED methodology.
- Increased their OEE by around 10 percentage points globally in less than a year.
Leveraging the impact of the Pulsar project, Genvamex decided to create a specialized area for the metal stamping presses. They added monitors and workstations with tablets and laptops for real-time monitoring of their machines directly from the shopfloor. With this change, they further reduced material transfer times and now effectively supervise the same 12 presses with 30% fewer labor hours.
Today, Genvamex uses Industry 4.0 technologies to monitor its presses in real-time and precisely control its operations. With Pulsar, Genvamex takes its industrial productivity to new dimensions of growth.
Benefits
Explore our platform
Explore more success stories
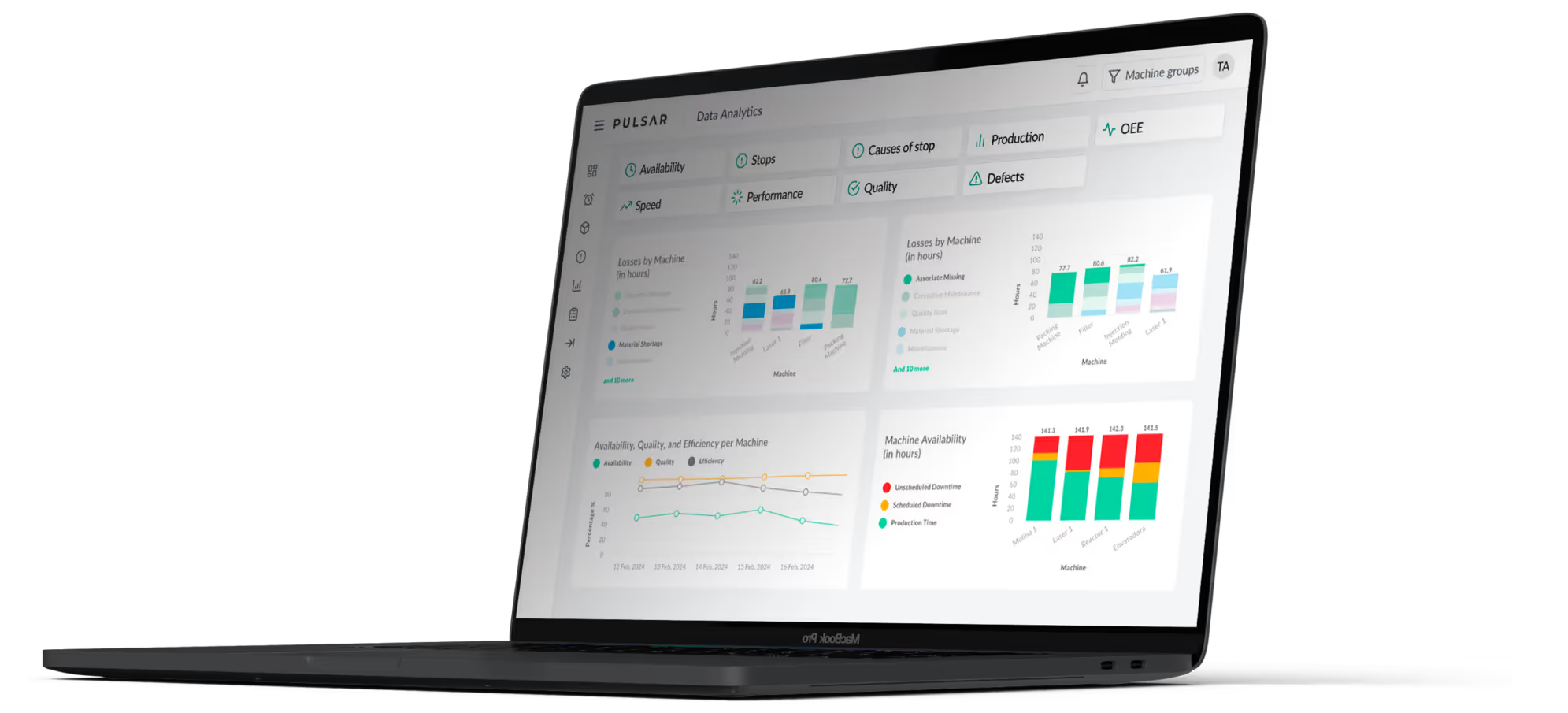
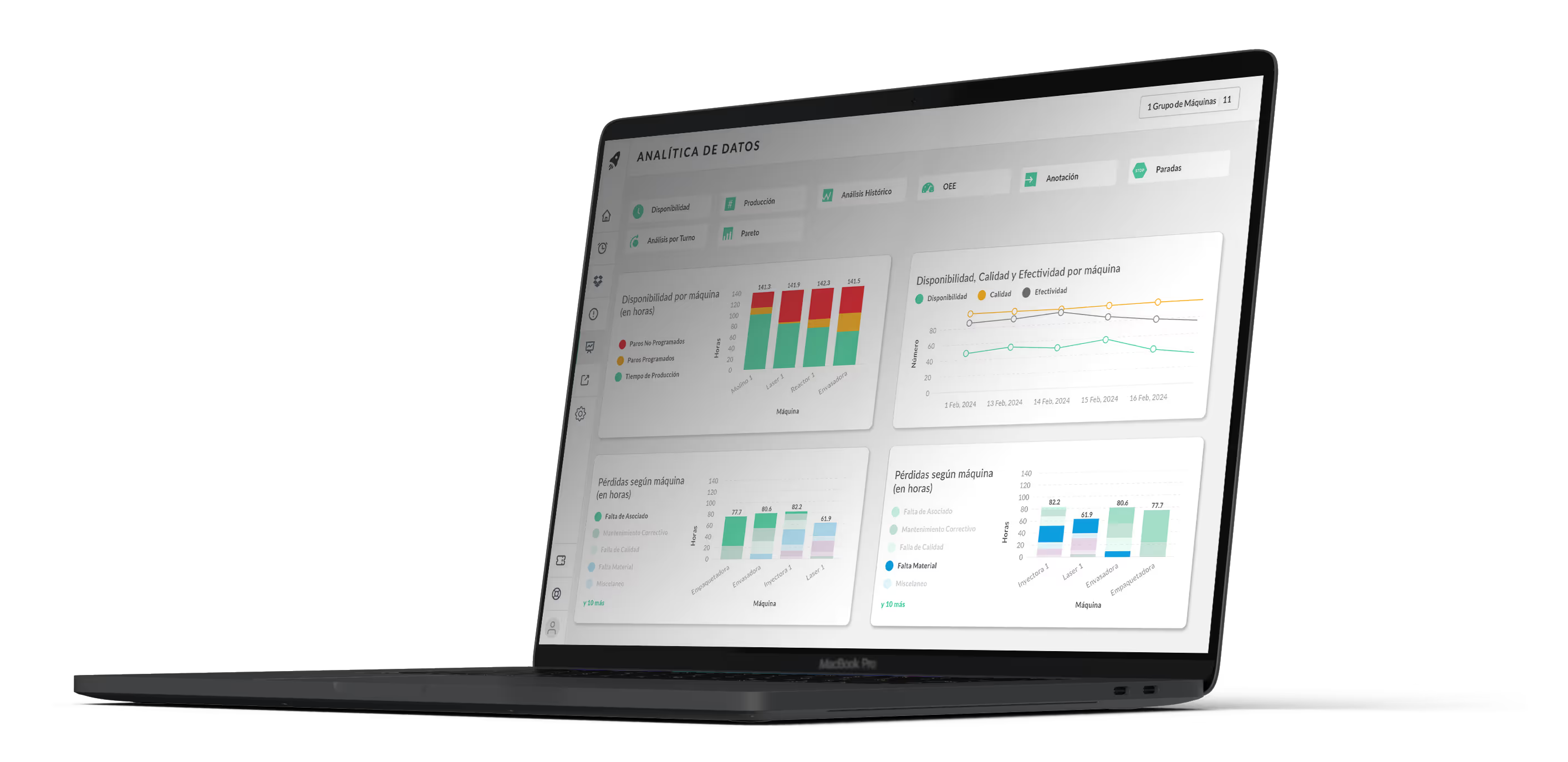
Request a Custom Demo
See how our production control and OEE monitoring platform can optimize your processes.
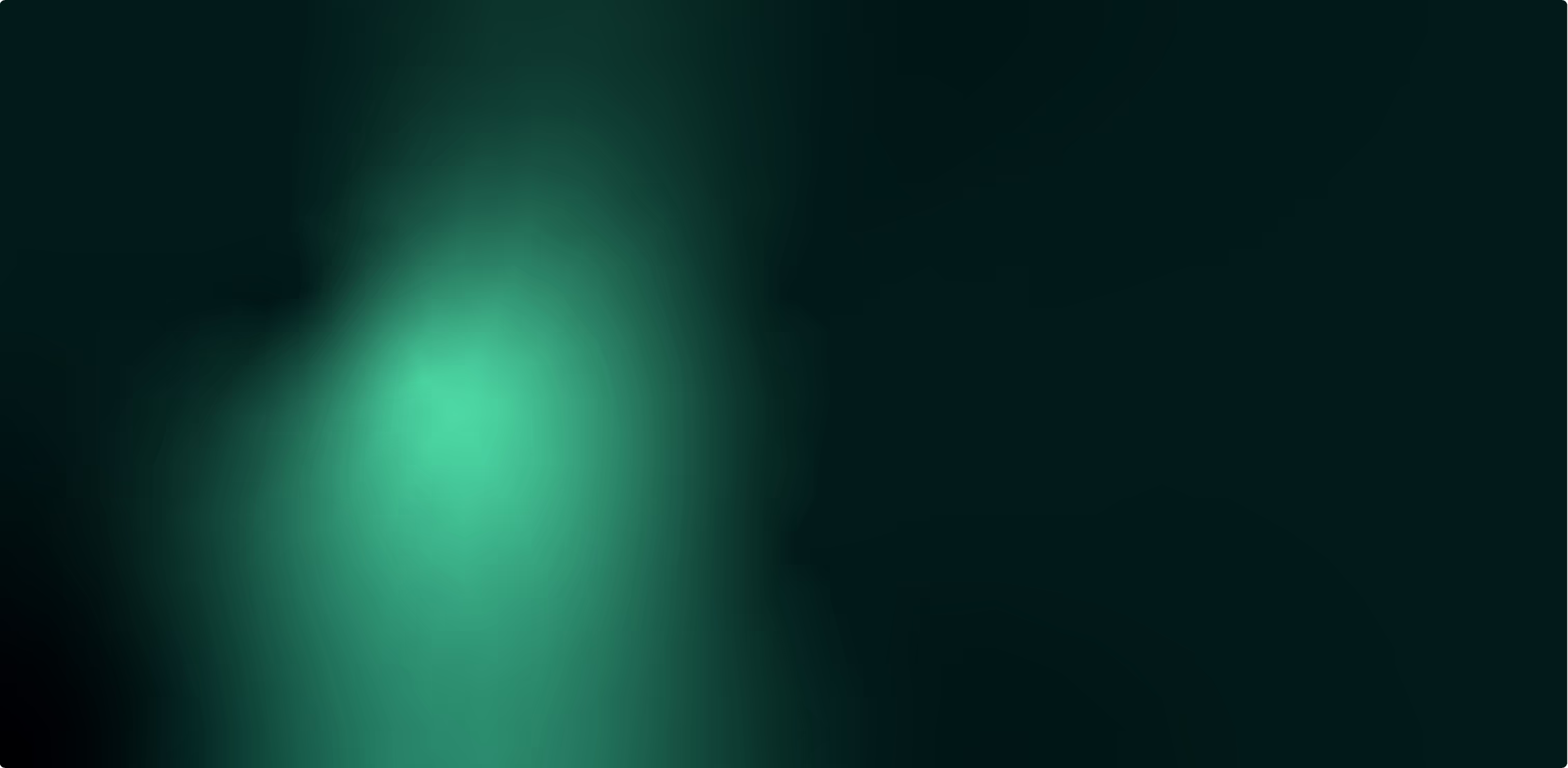